R_Lefebvre
Arducopter Developer
BT, nice work. Are you updating your design files as you go?
If you want to take a crack at some home made vibration dampers, I've been making these for a while. They are relatively trivial to make, but work very well. You can vary the amount of damping by changing the tube material used, and the wall thickness. I've used kevlar reinforced automotive hose that is fairly stiff. As well as non-reinforced silicon tubing, with latex tubing being the softest. I have some 1/2" OD, 1/16" wall latex tubing that is *rediculously* soft.
All you have to do is cut a short piece of hose, pierce it in two places, and push screws through. It is based on an industrial rubber ring damper, but I DIY in order to scale it for the load they are carrying.
If you want to take a crack at some home made vibration dampers, I've been making these for a while. They are relatively trivial to make, but work very well. You can vary the amount of damping by changing the tube material used, and the wall thickness. I've used kevlar reinforced automotive hose that is fairly stiff. As well as non-reinforced silicon tubing, with latex tubing being the softest. I have some 1/2" OD, 1/16" wall latex tubing that is *rediculously* soft.
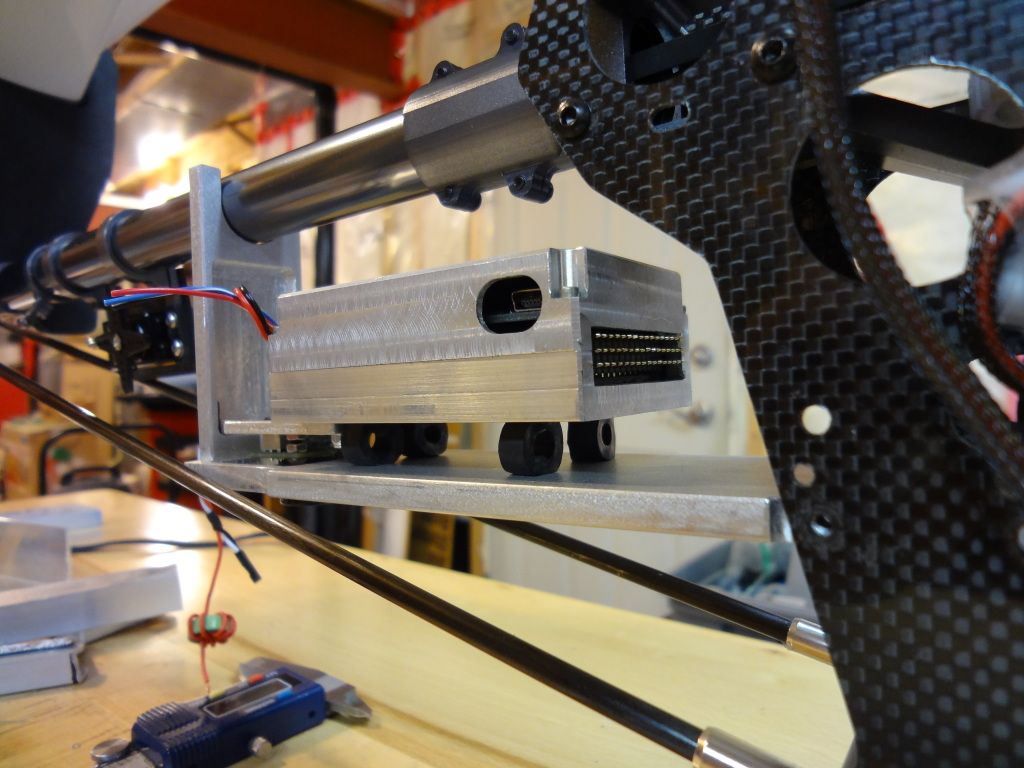
All you have to do is cut a short piece of hose, pierce it in two places, and push screws through. It is based on an industrial rubber ring damper, but I DIY in order to scale it for the load they are carrying.