So I am new to multirotors, but have been browsing the forums and reading everything I can for a while now. I have decided that I want to jump in to building one, and I want one stout enough that I can haul a go-pro camera now, and possibly upgrade to full FPV later. I was originally going to go with a bought frame, but being an industrial designer and mechanical engineer by career, with a full prototype shop at work, I decided that designing and building my own would be more fun/rewarding, and tailor it exactly to my needs.
I started thinking about the basic H or X frames, but the H frames worried me with their tendency to twist flex and transmit vibrations, and the X frames had the problem of the props being visible in the video.
So I had the idea to combine a simple X frame with a separate lightweight center frame (the I in the X-I name) to move the camera forward and the battery backwards, and to have that whole frame be heavily isolated from the motor booms for vibration resistance.
Theoretically, by mounting everything heavy and sensitive to a single frame structure, and then isolating that from the main motor/boom structure, it should provide extra vibration damping, while still being light weight and stiff.
That's the theory at least, so here are the pictures.
The main boom arms are home depot towel bars, while the plates making up the rest of the frame are 1/8in polycarbonate sheet, to be upgraded later to G-10 or CF. The rest of the hardware are off the shelf standoffs screws and washers from Mc-Master Carr (or the supply room at work)
The go-pro and battery are hung below the main frame, keeping the weight on the dampened section to help absorb any vibration that makes it through the rubber washers.
The feet are splayed outward to help protect the props in a crash
The main "I" frame is connected to the X frame solely just below the center of the X, while the rest of the frame does not contact.
In this cross section you can see how the X frame plates are attached to the I frame with a set of rubber washer shock absorbers. The amount of rubber will have to be tuned to give good rigidity while absorbing vibrations.
The motor to motor diagonal is 550mm, and according to my solidworks calculations, the frame should be around the 400g mark, with an AUW of around 1500g. Coming from the RC car world, and being a designer, I am also planning on designing and vacuum forming a lightweight lexan body shell, to protect the electronics, improve aerodynamics, and most of all, because it will look cool. That will come once I finalize the frame design. Should add very little weight, it will be very thin.
So that is my work in progress design. Currently all the cut pieces fit on a single 1'x2' sheet, so costs should be low.
The components I am planning to use so far are these:
Hextronic DT750s
http://www.hobbyking.com/hobbyking/store/uh_viewItem.asp?idproduct=6247
Turnigy Plush 25 amps (30s are out of stock)
http://www.hobbyking.com/hobbyking/store/uh_viewItem.asp?idproduct=2163
Hobbyking KK2.0 LCD board
http://www.hobbyking.com/hobbyking/store/uh_viewItem.asp?idproduct=24723
Slow fly 11x4.7 props (just linking one here, know I need 4 different ones)
http://www.hobbyking.com/hobbyking/store/uh_viewItem.asp?idproduct=22452
Various wires and connectors, USB programmer, Turnigy 9x, ect.
So, this is meant to be a combination build thread and discussion/critique, so I ask you, does this look like a good plan? Are my component choices ideal for what I am trying to do here? Is that combination of motor/prop going to work for me? What am I missing? Am I crazy and should go with something typical?
Like I said, I am new to this, so I need all the advice you guys can give me, thanks for the help!
I started thinking about the basic H or X frames, but the H frames worried me with their tendency to twist flex and transmit vibrations, and the X frames had the problem of the props being visible in the video.
So I had the idea to combine a simple X frame with a separate lightweight center frame (the I in the X-I name) to move the camera forward and the battery backwards, and to have that whole frame be heavily isolated from the motor booms for vibration resistance.
Theoretically, by mounting everything heavy and sensitive to a single frame structure, and then isolating that from the main motor/boom structure, it should provide extra vibration damping, while still being light weight and stiff.
That's the theory at least, so here are the pictures.
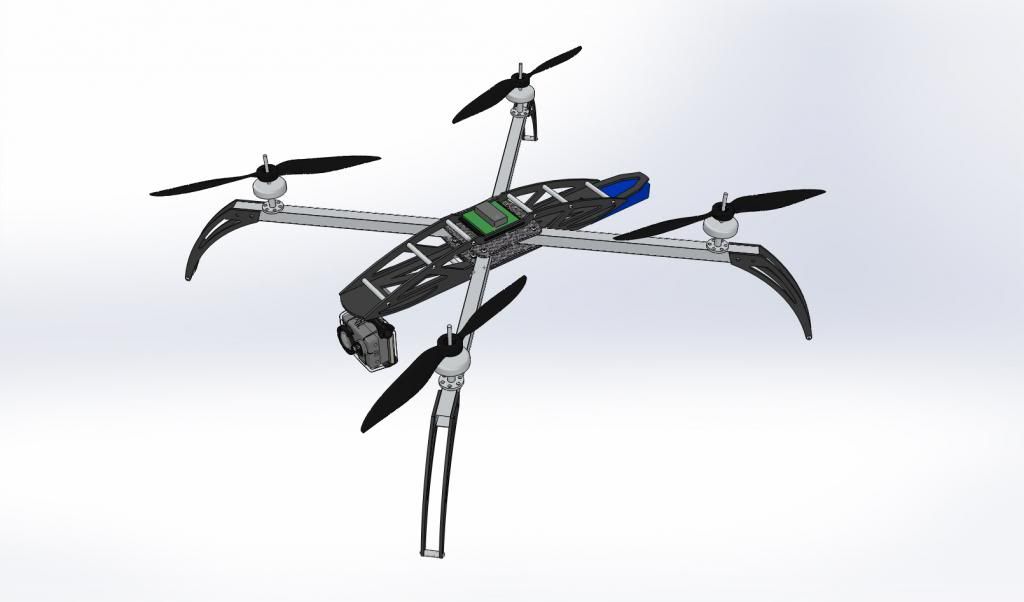
The main boom arms are home depot towel bars, while the plates making up the rest of the frame are 1/8in polycarbonate sheet, to be upgraded later to G-10 or CF. The rest of the hardware are off the shelf standoffs screws and washers from Mc-Master Carr (or the supply room at work)
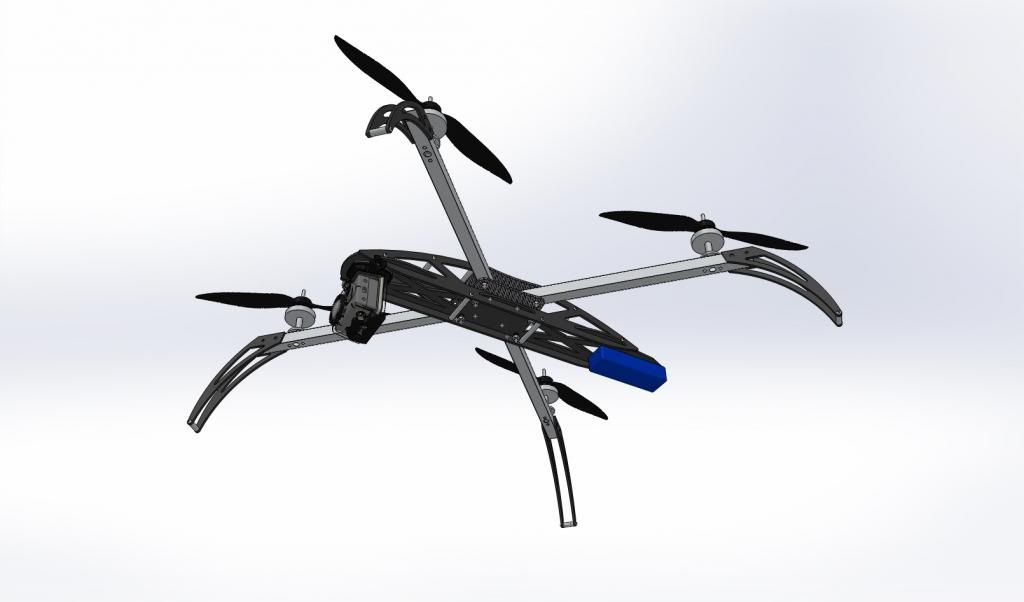
The go-pro and battery are hung below the main frame, keeping the weight on the dampened section to help absorb any vibration that makes it through the rubber washers.
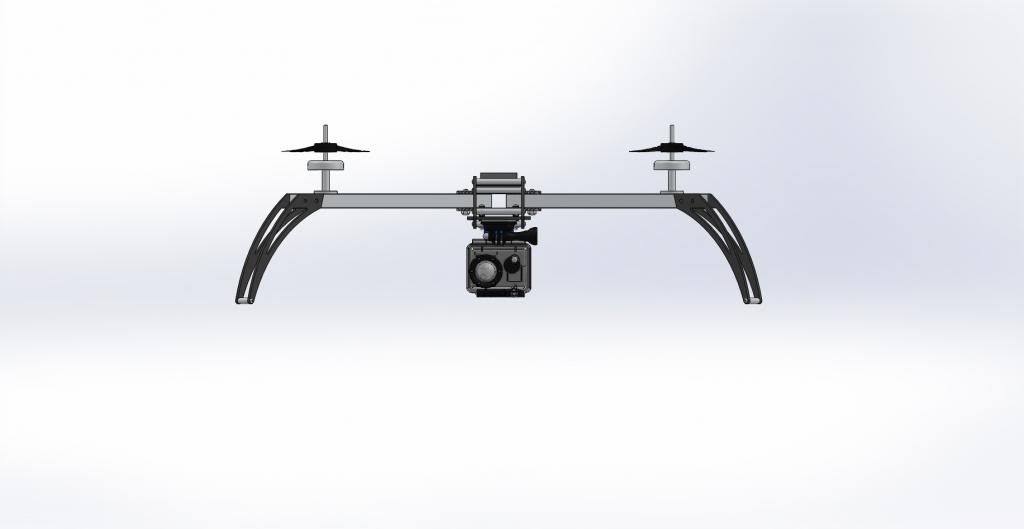
The feet are splayed outward to help protect the props in a crash
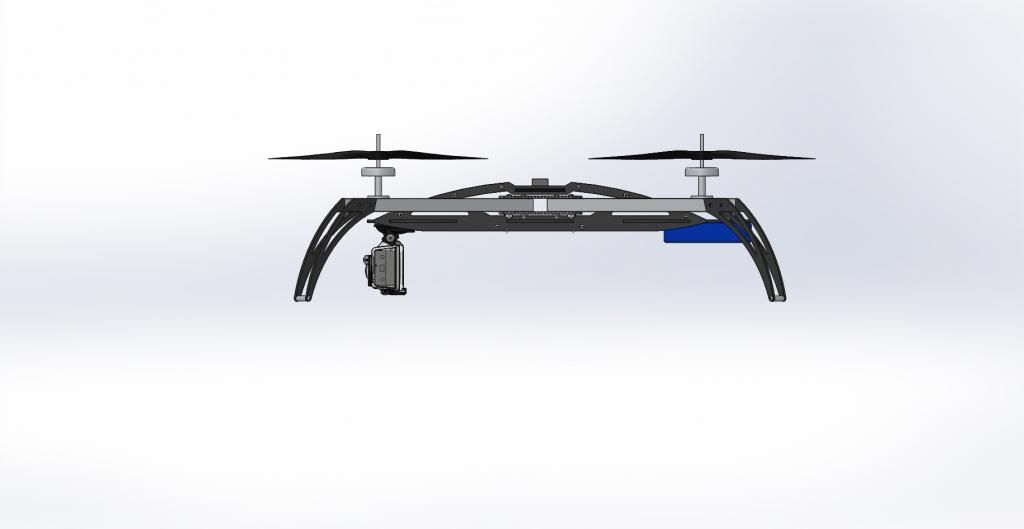
The main "I" frame is connected to the X frame solely just below the center of the X, while the rest of the frame does not contact.
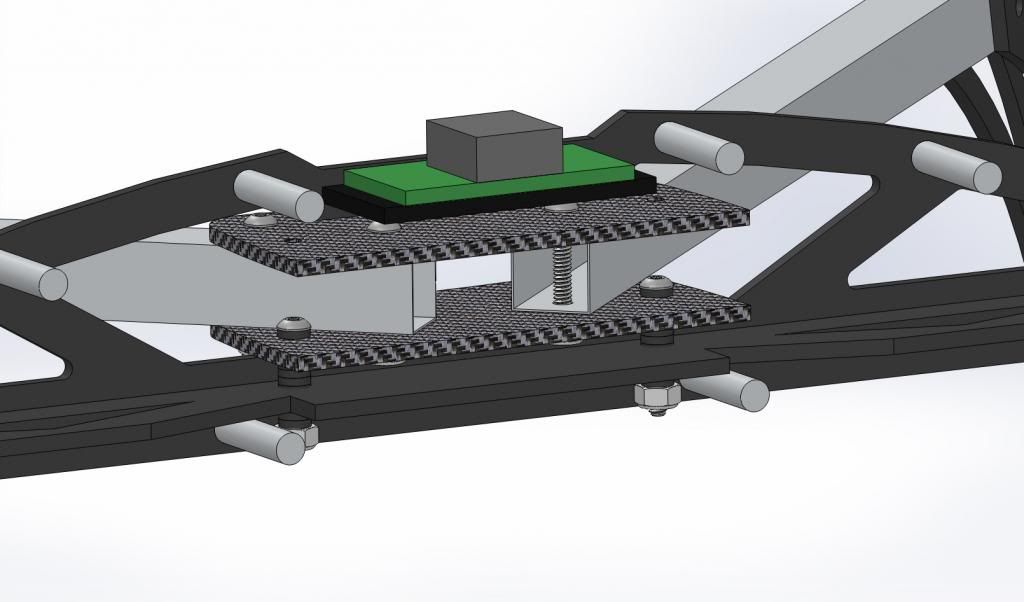
In this cross section you can see how the X frame plates are attached to the I frame with a set of rubber washer shock absorbers. The amount of rubber will have to be tuned to give good rigidity while absorbing vibrations.
The motor to motor diagonal is 550mm, and according to my solidworks calculations, the frame should be around the 400g mark, with an AUW of around 1500g. Coming from the RC car world, and being a designer, I am also planning on designing and vacuum forming a lightweight lexan body shell, to protect the electronics, improve aerodynamics, and most of all, because it will look cool. That will come once I finalize the frame design. Should add very little weight, it will be very thin.
So that is my work in progress design. Currently all the cut pieces fit on a single 1'x2' sheet, so costs should be low.
The components I am planning to use so far are these:
Hextronic DT750s
http://www.hobbyking.com/hobbyking/store/uh_viewItem.asp?idproduct=6247
Turnigy Plush 25 amps (30s are out of stock)
http://www.hobbyking.com/hobbyking/store/uh_viewItem.asp?idproduct=2163
Hobbyking KK2.0 LCD board
http://www.hobbyking.com/hobbyking/store/uh_viewItem.asp?idproduct=24723
Slow fly 11x4.7 props (just linking one here, know I need 4 different ones)
http://www.hobbyking.com/hobbyking/store/uh_viewItem.asp?idproduct=22452
Various wires and connectors, USB programmer, Turnigy 9x, ect.
So, this is meant to be a combination build thread and discussion/critique, so I ask you, does this look like a good plan? Are my component choices ideal for what I am trying to do here? Is that combination of motor/prop going to work for me? What am I missing? Am I crazy and should go with something typical?
Like I said, I am new to this, so I need all the advice you guys can give me, thanks for the help!